Maintenance scheduling is the action that helps define the frequency of equipment interventions. Accurately determining maintenance prevents production downtimes from happening, which, let’s face it, is not good for any company.
In the previous articles, we talked about the forms of scheduling by time: periodic and specific date. Today we will talk about a form of scheduling that begins to introduce a Condition-Based Maintenance (CBM) system, but which can still be understood as a form of periodic scheduling due to its accumulated characteristics. We are talking about Cumulative Scheduling. Understand this type of scheduling and how to plan it with the help of Engeman®. Follow!
Cumulative Scheduling
One action is strictly important for this type of scheduling to be correctly executed: data collection. These collections are based on a measuring point, which can be cumulative or trending.
A Measuring Point is an instrument used to determine measurements in equipment. The units of measurement for these Measuring Points calculate hours and kilometers/miles, among other factors that imply some form of measuring a period in which the equipment is in operation. They are essential for planning cumulative maintenance.
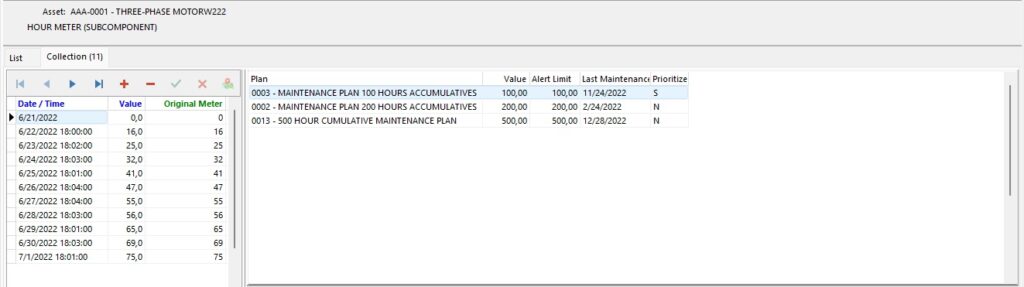
Engeman® Measuring Point
Cumulative maintenance schedules will be controlled by measuring the cumulative amount produced or used. Example:
- Maintenance is performed every 250 hours of operation.
- Maintenance was performed after a production of 20,000 tons.
- Maintenance is performed every 10,000 kilometers.
The collection is the evolutionary record of the measuring point numbers, with the date and time and the number corresponding to what is being detected at the point, such as an hour meter or mileage.
According to the collections, Engeman® calculates a trend line projecting the date of the next maintenance. Upon reaching an established maximum value, Engeman® will indicate the need for maintenance through the issuance of work orders.
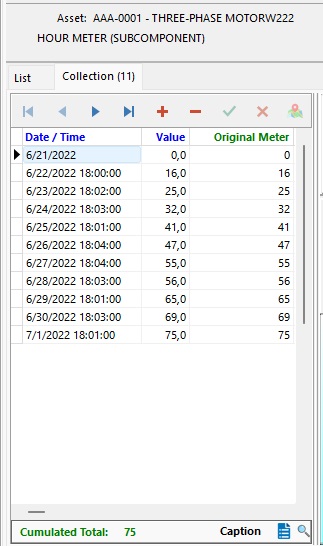
Engeman® Collections
Engeman® will manage the process of issuing work orders when more than one maintenance plan is scheduled, for the same point of asset, same performing department, and same date of performing. This fact happens when the scheduling parameters are multiple, for example, 250 hours and 1000 hours. In this case, the user may issue only the work order referring to the highest accumulated amount, as this may involve the activities of the 250-hour plan, thus rationalizing the issuance of documents.
The measurement of the data can be performed through manual notes or equipment intended for this purpose. And, it may be linked directly to the point of maintenance asset or portable for use at various points.
The success of using this maintenance scheduling process will depend on integrating the measured data with Engeman®. Both the system used and the measurement equipment must have tools that allow the creation of this interface.
Even if the data collection equipment is linked to other systems, the integration can be performed via database or web services with Engeman®. Usually, the systems that already have this data are those intended for planning and controlling the production process.
The information obtained over time creates a trend curve of the measured variable, which must be calculated via mathematical regression. This curve establishes a mathematical function of values x date, thus making it possible to determine the future maintenance date from the date on which the last maintenance was performed. If you request calculations for a longer period, Engeman® calculates the maintenance dates within the period, based on the mathematical function generated by the measurements of the first maintenance.
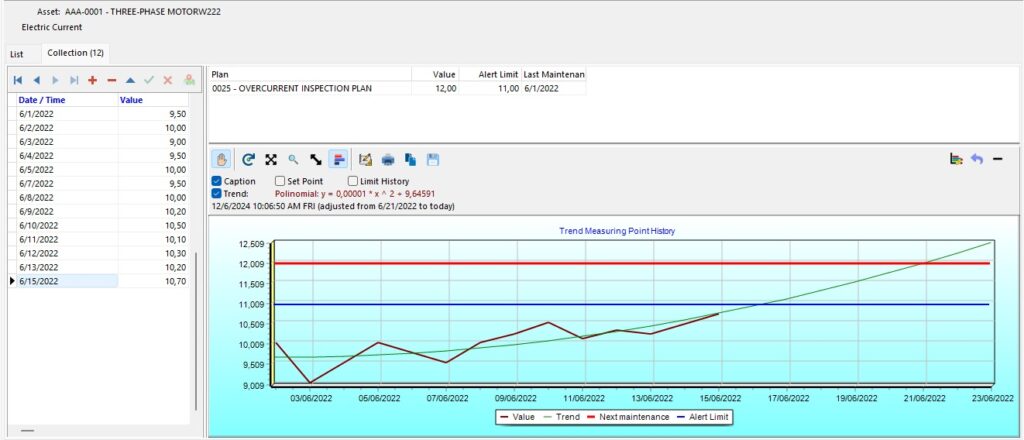
Engeman® Trend Collection
Necessary precautions for the use of this scheduling process
To perform scheduling by cumulative planning, it is necessary to take some precautions, namely:
- Measurements must be made systematically, which will require greater demand for resources and control of actions. Plans can be created with periodic scheduling to control this process;
- In the case of automatic measurements, verify the reliability of data collection and predict contingencies;
- Rationalizes the number of process measuring points;
- Creates approved documents for the manual data collection process;
- If more than one plan is applied to the same inspection point, establish multiple scheduling parameters;
- Engeman® identifies and corrects deflections in the trend curve generated by prolonged interruption, followed by a return to operation of the controlled equipment.
In addition to issuing work orders, Engeman® allows you to view measurements and future maintenance dates.
Engeman® Work Orders
Through measurements and typing of the cumulative numbers, Engeman® will calculate the Work Order performing date.
The W.O. closing automatically reschedules the next performing date, with no need to perform a new startup.
In the same way as the periodic schedule, Engeman® will issue consecutive W.O.s if the period requested by the user is long enough to allow the process. In this way, the first calculated W.O. will be based on real measurements, and the others will be calculated through the mathematical function established in the first W.O.
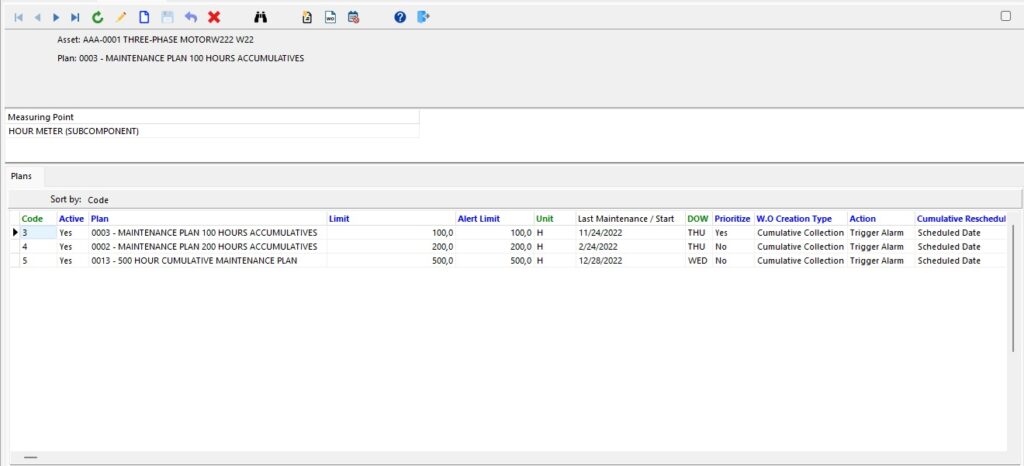
Engeman® Cumulative Scheduling
Screen Operations:
Schedule status: active or not – if it is active, Engeman® will calculate the W.O. for the schedule.
- Asset: equipment to which the maintenance plan will be applied.
- Location (TAG): a place where the maintenance plan will be applied, regardless of the asset. If there is more than one essay in the same location, one or more W.O.s will be generated for each of them.
- Limit the number of accumulated production or use a meter.
- Meter Previous threshold the number to anticipate the timing of W.O. Generation works only if the W.O. Generation Type is Accumulative Collection.
- Last maintenance date: date from which the plan will be started.
- DOW (Day of the Week): This field is informational only. Indicates the day of the week on which the last maintenance occurred.
- W.O. Generation type:
- Generation Screen: Engeman® will only generate W.O. on the W.O. generation screen. The calculation to achieve the maintenance goal will use linear regression.
- Cumulative Collection: For each collection posted to the measuring point, Engeman® will calculate the difference between the number posted and the number posted greater than or equal to the last maintenance date. It will not be checked on the W.O. generation screen.
- Cumulative Reschedule: choose the type of internal calculation that Engeman® will perform for the expected cumulative W.O. generation. According to the choice made, Engeman® will consider one of the dates below to restart the meter accumulator at the time of W.O. generation as the default values for the new relationships created between Assets and Plans through Cumulative Scheduling. Both the schedules calculated by the generation screen and those automatically generated by the collection will follow this configuration. The last maintenance date of the plans will be updated by this date.
Options are:
- W.O. Scheduled Date: Select this option to start the cumulative count from the scheduled date of a closed W.O., regardless of its performing or closing date.
- W.O. Closing Date: Select this option to initialize the cumulative count from the last employee record date (if it exists) or the W.O. close date (when there is no employee record). In this way, a W.O. that has its performing date well after the scheduled date will be able to better “adjust” the planning.
If you use the Prioritize “Yes” option, the plans with the lowest limit will obey the configuration determined by the plan with the highest limit that uses the Prioritize “Yes” plan. Using the Prioritize “No” option, the choice of options is independent.
- Start plan by Fixed Limit: This option refers only to the Generation of Work Order by Cumulative Collection and does not influence the generations of the Generation Screen. Choose this option to start the plan when the fixed limit is reached and not the accumulated limit. Example:
- If the fixed limit option is No and the plan limit is 1500 km, with the last maintenance occurring at 3300 km, the next maintenance will only occur at 4800 km, so 1500 after the last maintenance.
- If the fixed limit option is Yes and the plan limit is 1500 km, with the last maintenance having occurred with 3300 km, the next maintenance will occur with 4500 km because this will occur respecting the fixed limit of 1500, disregarding that the last maintenance occurred 300 km later.
Action:
- Alarm: Only for the Cumulative Collection type. Upon reaching the goal, Engeman® will display an alarm message and ask if Engeman® should generate an early W.O. for this maintenance plan. After the W.O. is generated, the user can still print the generated W.O. or view it on the screen.
- Generate W.O.: Engeman® will generate a W.O. without emitting any visual warning, only an audible warning.
- Generate and Print W.O.: Only for the Cumulative Collection type. Engeman® will generate W.O. and then print it automatically.
- Generate and View W.O.: Only for the Cumulative Collection type. Engeman® will generate W.O. and then view it automatically. This option is important in the case of giving feedback to the user on the generation of the W.O. It also allows the user to send the W.O. by e-mail or even print on another printer other than the standard.
- Prioritize: If the YES value is checked, then plans with greater frequency will prioritize this relationship (if this option is checked on the W.O. generation screen). Otherwise, regardless of the marking of the W.O. generation screen to prioritize, Engeman® will not prioritize this plan. For plans with automatic generation by cumulative collection, Engeman® will prioritize only if this option is checked for YES. If the option is NO, then the plan will always be generated. Only plans with the same performing departments will be prioritized.
The prioritization of cumulative scheduling does not consider the multiplicity of numbers, as happens in the periodical. However, when generating a W.O. for a higher value plan, all lower number W.O.s are prioritized if in the relationship between the plan and asset the option PRIORITIZE=’YES’ and at the time of Generation the prioritization option is checked.
To view which are the Competing Plans of an asset, just click on the “Display Competing Schedules” button.
Concurrent Scheduling
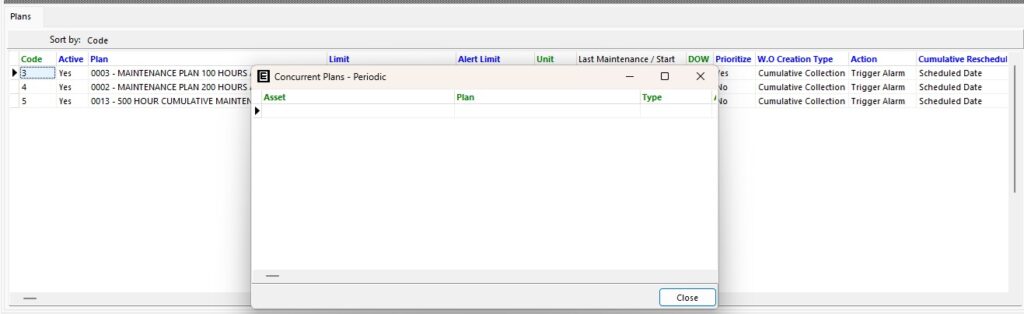
Engeman® Concurrent Plans
Concurrent scheduling implies the W.O. generation for an asset with the same plan registered in 2 or more different types of scheduling. The goal is to ensure that the system generates only one W.O. for this plan and for this asset, that is, only in the scheduling that happens first.
The system understands concurrent scheduling as how plans are associated with assets. For example, a P001 plan is associated with an A001 asset through cumulative scheduling to generate W.O., every 500 units. If the same plan P001 is associated with the same asset A001 but by periodic scheduling, to generate W.O., for example, every 3 months, at the time of generation the system will check which of the two situations will happen first and will generate the W.O.
During maintenance, while this W.O. is open, no other W.O. will be generated for this same asset and this same plan on any other schedule, even if it has already reached the limit for a generation. Upon closing the W.O., all schedules containing this plan and this asset will be rescheduled according to the scheduled or closing date of this W.O.
In the cases above, the same plan was associated with the same asset but in different schedules. Consequently, the system must generate W.O. every 7 days (periodic) or every time the cumulative collection reaches the limit of 1000 hours (cumulative). Therefore, suppose the limit of 1000 hours is reached. The system will generate the W.O. normally, and if it is not closed, no other periodic W.O. with this plan will be generated.
When closing the W.O. of a concurrent plan that was generated on a cumulative scheduling, the last maintenance date will be updated on both periodic and cumulative and any other schedule where this plan is associated with this asset.
One obstacle is that the periodic schedule will be rescheduled for the day of the week on the date on which the cumulative scheduling was scheduled or closed. This will make Engeman® not generate W.O. in a loop because the W.O. generated by the periodic in a previous generation would no longer make sense. After all, the cycle will have been altered. In this way, all these W.O.s would be automatically canceled so that the system can generate again from the new date, following the new cycle.
Conclusion
Wow, I know, that’s a lot of information, but don’t worry; all you’ll need to know when using Engeman® is that these actions will be managed by it and reported to you. That is why it is so important to have software that is an expert in maintenance.
Our implementation team, developers, and analysts have already gone through a series of situations, and this means that Engeman® always has solutions to the problems and situations of day-to-day maintenance.
In the next article of the series, we will continue talking about condition-based maintenance, however, talking about a world totally oriented to data and prediction, Scheduling by Trend.
Until then.
Also, follow the first articles of the series:
- Maintenance Scheduling at Engeman®: 1st – Periodic – Time-Based Maintenance (TBM)
- Maintenance Scheduling at Engeman®: 2nd – Specific Date – Time-Based Maintenance (TBM)