It is undeniable that a good manager schedules all the activities of his team systematically. After all, large companies tend to have a large amount of assets, and, therefore, it is essential to have adequate planning to be able to cover all these materials.
Knowing that maintenance is a crucial factor for a company’s proper functioning and profitability, management needs to ensure the performance of all its equipment to ensure the quality of products and compliance with customer deadlines. Managing an entire maintenance department only in spreadsheets is very risky for any business. You lose out on data reliability, reporting, and data analysis time.
Today we start a series of articles where we will show you how to perform maintenance scheduling efficiently with the help of Engeman® software. Don’t miss any articles on how to have successful management!
The Engeman® software
Engeman® is a maintenance software aimed at maintenance managers and operators who want a complete solution to efficiently manage processes such as documentation control, service planning, analysis of causes and effects of occurrences, travel control, and other features.
It is flexible software that adapts to your company’s realities. It offers options for WEB, Mobile, Cloud, Client/Server, and several other resources for your management to schedule the department’s activities strategically.
And it is possible to perform several types of schedules according to your daily demand or types of assets. See below how to perform Periodic Scheduling at Engeman®.
What is Time-Based Maintenance?
Time-Based Maintenance (TBM), also called Periodic Maintenance in Engeman®, refers to routine maintenance tasks performed on an asset at fixed time intervals, regardless of its condition.
As a preventive maintenance type, the goal of time-based maintenance is to prevent failures before they happen and improve asset performance. However, because it can be accomplished whether it is necessary or not, it does not always register a balance between risk and return.
For example, changing your car’s oil every 5,000 kilometers, as opposed to the 10,000 km recommended by the manufacturer, may lead to fewer problems, but it comes at a cost. While a lower risk of failure can be a return, money and time are wasted performing oil changes more frequently than recommended.
Even so, periodic training can be beneficial when used as part of a larger maintenance management strategy, as it requires minimal training since time-based tasks are relatively simple and typically do not require extensive training to learn.
Advantages of Time-Based Maintenance (TBM)
Periodic Scheduling has some benefits, such as:
- It may present a lower cost in the long run since, compared to emergency corrective maintenance, time-based maintenance is relatively inexpensive;
- It is easy to implement, as it does not require additional sensors or equipment to decide when assets need maintenance;
- It is predictable because, by following a defined time interval, maintenance schedules are consistent and calculated;
- It is effective for continuously running assets where increased wear is more likely, allowing maintenance work to be scheduled at regular intervals.
Periodic Schedule at Engeman®
In Engeman®, it can be managed, and due to its characteristics, the generation of derived work orders can even be generated by scheduling, providing expected schedules and costs that are very useful for maintenance management.
Let’s see how a maintenance plan can be periodically programmed within Engeman®:
First, we will need to have an Asset and a Maintenance Plan previously registered. We will not go into these register details here.
A good place to define periodic maintenance is on the Maintenance Plans screen.
On this screen, click on the button for
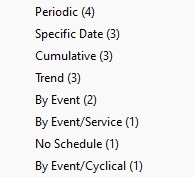
Engeman® Periodic Menu
Then we define in which equipment or locations the maintenance plan in question will be scheduled periodically and the specific periodicity of each one.
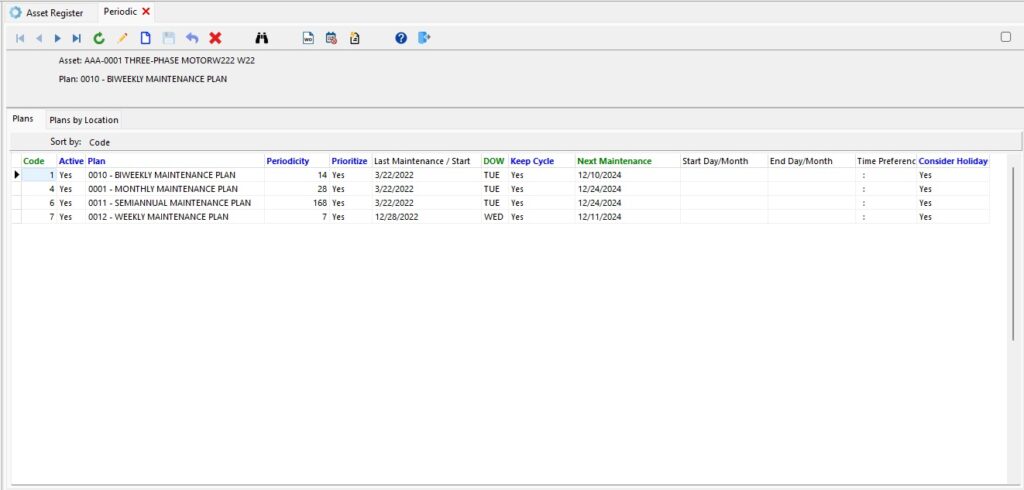
Engeman® Periodic Screen
This scheduling process is simple and efficient and does not require a control structure to perform since it is performed entirely by the computer. It is enough for the user to provide the period, only once in the startup of the plan, indicating the date of the last or next maintenance, then the calculation of the other performing dates of the plan will be performed automatically.
Engeman® will manage the process of issuing work orders when more than one maintenance plan is scheduled for the same point of asset, the same performing department, and the same performing date. This fact happens when the scheduling parameters are multiple, for example: weekly (7 every 7 days) or monthly (28 every 28 days), where 28 = 7×4. In this case, the user may issue only the work order referring to the highest periodicity, as this may include the activities of the weekly plan, thus rationalizing the issuance of documents.
Periods can be established according to the manufacturer’s instructions. However, there will always be the need to adapt to the period with the availability of human resources. A process that facilitates periodic scheduling is the determination of multiple periods of 07 days, enabling:
- Scheduling services on predetermined days of the week;
- Scheduling services outside weekends;
- Scheduling services, with different periods, on the same date, for the same point of asset.
How do you define Time-Based or Periodic Maintenance?
Periodic scheduling should be versatile, allowing the manager to modify it. The tendency of these changes, in most cases, will be to increase the period, which is a natural consequence of the benefits of well-performed maintenance systematically.
The days of the week scheduled for the various periods may or may not coincide. E.g., weekly, monthly, and semiannual maintenance—On the day of semiannual maintenance, monthly and weekly maintenance should also be performed. Engeman® will issue a single work order, describing the procedures to be done.
Once the parameters have been determined, work orders can be calculated and issued. Their closure automatically reschedules the next performing date, with no need to perform new startups.
Engeman® allows the consecutive issuance of more than one W.O. referring to the same plan and the same schedule within a period established by the user. Example: If the schedule is 7 days and the requested period is one month, then at least 4 W.O. will be issued to the asset point.
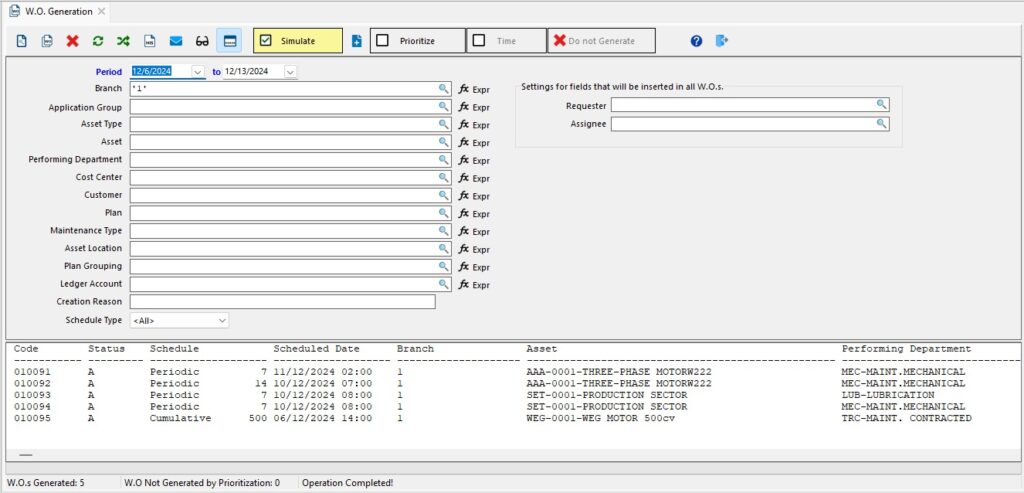
Engeman® Periodic Generation Screen
Two things are significant in Engeman® periodic scheduling:
Prioritize: This field has the default value to prioritize = yes. When prioritization is marked with “yes,” it means that plans with the lowest number of recurrences will be excluded in favor of plans with longer recurrences; that is, a 7-day maintenance plan will be excluded if a 14-day maintenance plan is scheduled for the same date. This is because, generally, plans with a higher number of periodicities contain, in their checklist, all the operations that should be performed in plans with lower periodicity, thus reducing the number of W.O.s issued. For a plan to be issued, regardless of prioritization, mark this field with the value “not” prioritize.
Maintain Cycle: Even if a work order is placed outside the scheduled date, Engeman® may maintain the original scheduling dates so as not to harm other existing schedules. To do this, the “Keep Cycle” option must be marked with S (Yes), for example:
- Weekly schedule period = 7 days
- Expected date for maintenance: 07/13/2024
- Effective Date (W.O. Closing Date): 07/16/2024
- The last maintenance date for scheduling purposes is 07/13/2024
- Date of the next maintenance calculated by Engeman® = 07/20/2024
If the “Maintain Cycle” option is marked with N (No), Engeman® will calculate the date of the next maintenance from the W.O. closing date, that is, 07/16/2024, and the next maintenance will be 07/23/2024.
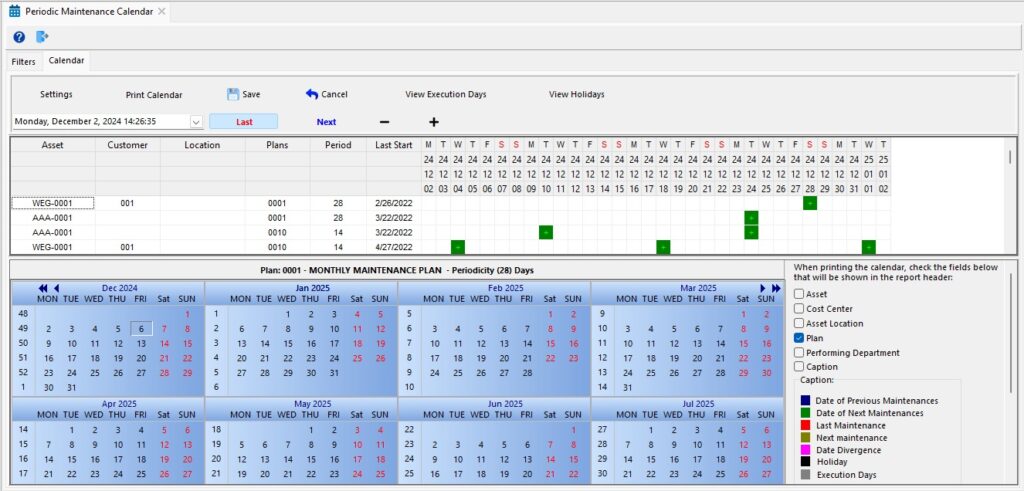
Engeman® Periodic Calendar Screen
I believe that with this information it will already be possible for you to generate numerous periodic maintenance schedules.
Conclusion
Engeman® software, which is specialized software in maintenance management, is an essential tool for your team to schedule all their maintenance with the reliability and agility that the high competition in the market today demands. In this article, we have seen how important the Periodic Maintenance Schedule – Time-Based Maintenance (TBM) is and how to perform it within Engeman®.
In the next article, we will continue talking about Time-Based Maintenance (TBM), however, we will be dealing with the form of scheduling by “Specific Date” in Engeman®.
See you there!